Grinder Pump Driven Pressure Sewer Systems
Failing septic systems nationwide and the Clean Water Act helped spur the development and adoption of a system that revolutionized wastewater collection and transport. Since the days of the Roman aqueducts, common sense dictated that wastewater always ran downhill. In the latter half of the 20th century, a new technology changed that reality. Previously orphaned sites that existed in areas of high water table, below grade or heavy rock strata could now be sewered economically and in a more environmentally sensitive manner.
The low-pressure sewer (LPS) system, also known as a pressure sewer, consists of a network of pressure pipes and grinder pumps, which may be installed at each home site. The grinder pumps collect all wastewater from the home and grind it into slurry. The wastewater is then pumped to a larger sewer main or directly to a wastewater treatment plant.
Grinder pumps were first developed 40 years ago. Today's state-of-the-art grinder pump is more reliable and durable than ever before.
The modern pressure sewer system employs sophisticated technology known for its reliability, minimal maintenance, low upfront costs, reduced operating expenses and ability to be installed at any site, regardless of topographical challenges.
It uses an unobtrusive small-diameter pipe installed below frost line and conformed to the natural topography. Unlike conventional gravity central sewers, which can use up to 24-inch pipe and require deep excavation, the pressure sewer system employs small diameter 1½- to 6-inch pipe, and is not destructive to natural or built features.
Case Studies
Athens, Tennessee
The inadequate, aging conventional gravity system could no longer handle the amount of wastewater produced in Athens, Tenn., a small rural town of 14,128. The increase of water infiltration and inflow levels made things worse.
Athens faced a daunting task, and the situation was dire. "The town had been under a state-ordered sewer connection moratorium since 1990, preventing much needed growth of industry, manufacturing and population," said Wayne Scarbrough, Athens Utility Board (AUB) assistant general manager.
A $20 million wastewater treatment facility renovation, completed in 2005, was part of the solution but was still not sufficient. One town project was particularly effective in eliminating infiltration and inflow. Rather than exchange the archaic conventional gravity array with a newer version of the same technology, the AUB opted to abandon the old for an alternative replacement in a particularly problematic, wastewater-challenged section of town.
"Rainwater run-off that bypassed the pump station contributed considerably to the problem, especially in spikes during wet weather flow. We had to replace the gravity system and decided on a low pressure system with grinder pumps," said Randy Harrison, AUB wastewater construction supervisor.
"Because we installed smaller mains, construction was much less intrusive on our customers and in some cases not recognized except for the installation of the [grinder pump] station. Using the grinder pump system we have now permanently eliminated all infiltration and inflow," said AUB Superintendent Jill Davis.
Not only did it reduce operational costs, but this low pressure scheme also yielded savings in excavation, infrastructure and materials costs and minimally disrupted the surrounding area.
The sewer system was well suited for the Athens application. The individual grinder pumps installed at each site that push slurry wastewater from homes, businesses, a school and a church eliminated the need for costly lift stations.
The system costs significantly less to install and operate than a gravity system and requires less maintenance. "The Athens abandonment project has been operational for more than two years. There have been virtually no problems and little service or maintenance required," said Davis.
Pump station records verify that 700,000 fewer gallons were eliminated from wet weather spike flows in the first year after installation. In 2003 there were 500,000 gallons of water overflow from nine events; in 2007 there were zero gallons and zero events.
"Our records also indicate a reduced flow through the pump station to our treatment plant of 27.5 million gallons per year, with a yearly savings of $89,212 in treatment cost alone. Eliminating overflow levels, which are state violations, helps our standing with state regulatory officials," said Harrison.
"The construction savings by choosing the pressure sewer system was 25 to 35 percent. The actual cost included abandonment of the old gravity main, which would have been required regardless of the technology chosen."
"The low-pressure system has needed little time or attention and savings from reduction of wastewater infiltration and inflow through the treatment plant is significant. Pump run time is also greatly reduced. Maintenance time for stopping to clean the system has diminished and less overtime will likely produce additional savings," said Davis.
Marion, Massachusetts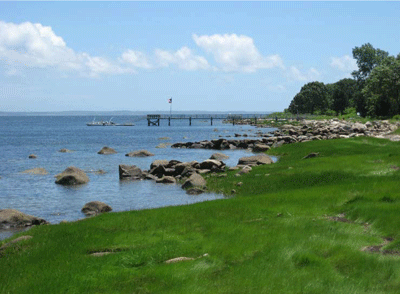
Rocky soils, sandy soils, high groundwater, variable terrain sloping and draining toward the waterfront create significant geo-technical challenges that make conventional wastewater disposal methods obsolete. With small lots built to capacity and packed tightly together, the coastal town of Marion, Mass., needed a solution that created maximum density for wastewater infrastructure.
In 2004, when Marion undertook an expansion of its sewer systems, it selected a low-pressure sewer over a traditional gravity system. With only shallow trenching required and no inflow, LPS was a good option. The challenges of the terrain helped steer the decision toward LPS, along with ease of design, installation and lower-cost operation and maintenance (O&M). Since Marion had 455 homes in three shoreline neighborhoods, this project became the largest single-contract LPS system in New England.
Residents, however, were concerned with the cost of installation and O&M and had some mixed history with earlier systems. The design and installation firm, Earth Tech Inc. from Long Beach, Calif., thoroughly involved the community through ongoing town meetings, communications and consultations. The residents were treated as stakeholders in the project. The proposed LPS system was widely accepted, so a proposal was presented that the town purchase, install and maintain the pumps for the entire project. This proposal included a five-year manufacturer's warranty and a ten-year service contract from the town for all private property installations. The voters accepted the proposal.
The manufacturer of the specified grinder pumps and its Rockland, Mass., representative, F.R. Mahony & Associates, negotiated with the town of Marion and provided a favorable warranty and service agreement. The manufacturer would provide free repairs onsite and free required maintenance during the warranty period.
The project was completed in October 2006. Servicing the 455 homes saved more than 40 percent compared to the gravity alternative. The project was completed in half the time of the gravity proposal and resulted in more than 22 percent savings over what was planned in the construction budget. With only minimal non-startup service calls since installation, Marion considers this a successful project.
Conclusion
Hundreds of thousands of successful installations worldwide show that what was once considered a sewer alternative is now a sewer choice, especially in communities that have flat, hilly, rocky or wet terrain. With municipal budgets challenged more than ever and sensitivity toward carbon footprint increasing, the grinder pump-driven pressure sewer is a lean and green option.